盲孔树脂填充(IPC-600G)
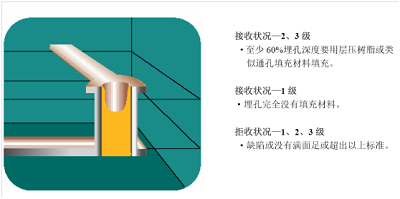
埋盲孔孔铜厚度要求(IPC-6012B)
薄板电镀
多次电镀,铜厚均匀性及蚀刻难度增加
盲孔与通孔的对准度
翘曲度
两次及两次以上压合时,内层芯板的收缩
盲孔填胶
盲孔除胶
四 埋盲孔加工过程控制的要点
内层钻孔
叠板时板需平整,不可有弓曲
加工时压脚需压紧铝片,防止产生较大毛刺
薄板(<3mm)打磨时用硬板垫在下面,防止打磨变形
内层沉铜、加厚
沉铜前磨板机清洗
全板镀时<5mm芯板使用薄板框加工
全板镀后全部用1500#砂纸打磨
孔铜厚度根据IPC标准进行加工,工程MI将要求铜厚注明清楚
内层图形、检验
前处理磨板时需做磨痕测试,<15mm板在IS机过微蚀再在宇宙磨板机上开第一组磨刷轻磨加工,保证板面不可有氧化。
对位时居中对称,保证板边四角对位PAD不可有破环现象。
检查板四角对位PAD不可有破环现象。
压合
薄板注意调整空铆高度。
钢板清洁,防止凹痕内的胶除不净。
离型膜不可有皱折,流胶太多,影响除胶效果
钻靶时盲孔层朝上钻靶。
钻靶时每5PNL翻面检查有无偏位现象。
盲孔填充不可使用S1000B及S1000-2B的PP。
除胶
盲孔除胶在沉铜做去钻污处理,去钻污后再在宇宙磨板机上磨板处理
未去除干净的板只可手工打磨
微蚀
微蚀前抽测板面铜厚,如有差异(板面平均值间≥10um),分类微蚀。
微蚀前首件确认参数,保证微蚀次数为偶数次,并微蚀时正反面所过次数一致。
微蚀时抽测板面铜厚,如有异常,及时停止加工,重新调整加工参数。
微蚀时按PNL数添加药品,保持微蚀液稳定。
钻孔
装板时双手执板,水平套入定位钉,不可强拍套入,防止损坏靶孔。
加工前首件检查测试孔,确认偏位和收缩情况,如有破环,通知工程师处理。
外层图形、检查
使用黄片对位,十倍镜检查通孔与盲孔的对准度,参考板边四角的盲孔对位PAD。
外层检查时用十倍镜检查盲孔的对准度,不可破环。
蚀刻
蚀刻前先找出并测量最小线宽,做首件确认合格后再生产。
加工时注意检查盲孔边缘和BGA处的蚀刻效果,防止出现欠腐蚀和蚀刻不净的现象。