
[导读]
沉金工序在生产101309C08A时出现渗金造成IC间距减少超过20%报废两批板,其报废面积为4.1平米,其制程特性为表铜>71um,黑色阻焊油墨。
一、 背景:
沉金工序在生产101309C08A时出现渗金造成IC间距减少超过20%报废两批板,其报废面积为4.1平米,其制程特性为表铜>71um,黑色阻焊油墨。
二、目的:
验证厚铜板过微蚀对蚀刻毛边的影响,以确认表铜>70um的厚铜沉金板是否需要过微蚀,以降低毛边长度,达到降低沉金厚铜板渗金报废的目的;
三、结论:
1、蚀刻正常,用10倍镜看不到蚀刻毛边的板子,过微蚀对蚀刻毛边改善效果不明显;
2、目前厚铜板产生渗金的主要部位为阻焊侧蚀区与PAD的间隙,渗金与蚀刻毛边的关系较小。
四、试验方案:
1、取表铜厚度要求>91um报废板25071,取同一片板分为不同次数过喷锡线微蚀前处理;测定微蚀速率为约1.2 um/min的情况下以1.9m/min的速度(微蚀量约0.8um),分别切取过微蚀0次、1次、2次后IC位垂直切片并测量线底、线顶线宽变化量,并计算蚀刻因子;
2、从MRB挑取表铜>71um的报废板,做IC位的垂直切片,观察渗金与蚀刻毛边的关系;
五、试验结果:
1、不同微蚀量下IC位线宽变化如下:
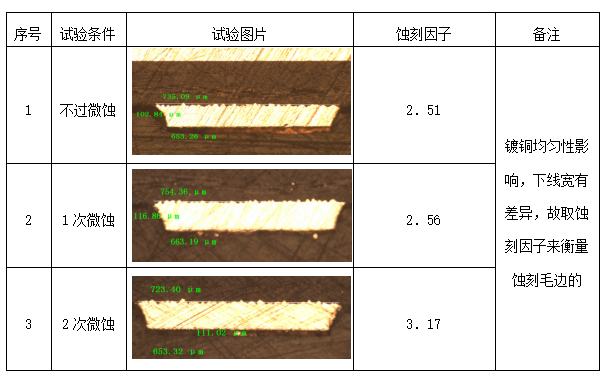
小结:从实验的数据分析,过微蚀两次的可以提升蚀刻因子由2.51提升到3.17,折算为70um表铜厚的板子可以增加6um的线距,而70um铜厚厂内制程能力IC间最小间距为0.34mm(补偿值为0.16mm,开窗0.05mm,阻焊桥0.08mm),则影响到的线距仅为6/340*100%=1.8%,即针对目视无毛边的板子,过微蚀对IC间间距的影响较小,建议不采用。
2、取MRB报废的厚铜板(表铜>70um),打切片观测IC位渗金与蚀刻毛边的关系,切片图片如下:
小结:从随机选取的几个厚铜板IC位切片看,蚀刻毛边较小,渗金的部位为阻焊侧蚀区与PAD的间隙。
六、改善方向:
厚铜板IC间的阻焊较厚,其显影侧蚀较大,如何减小侧蚀及减少侧蚀下面活化液的残留需工艺跟进解决。

【推荐阅读】:

责任编辑:LISA
创盈电路 版权所有:http://www.cwinpcb.com/ 转载请注明出处